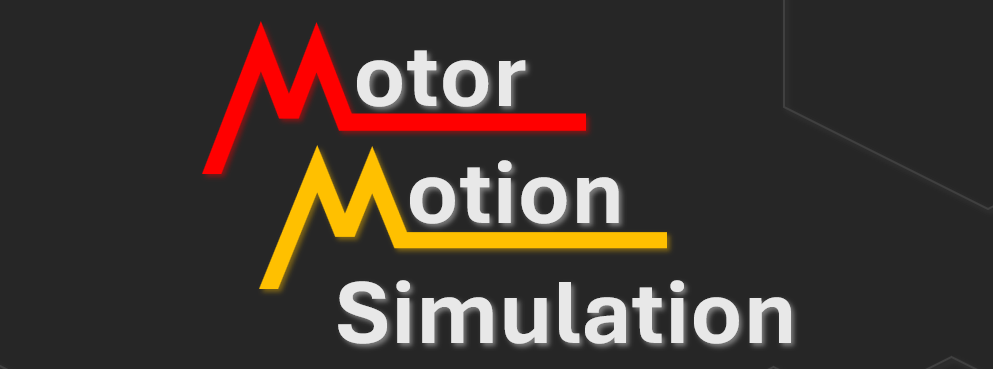
Drive innovation with precision with Motor Motion Simulation. Simulate, analyze, and optimize motor and machine performance for superior engineering outcomes. Sodick America’s Motor Motion Simulation software allows for risk mitigation, cost efficiency, design optimization, and time saving. This innovative solution can simulate not only how a motor will react and behave, but how it affects the machines structure as well.
Why choose Motor Motion Simulation?
- Risk Mitigation
- Simulation allows engineers and designers to identify and rectify potential issues in a virtual environment before physical implementation.
- Cost Efficiency
- Simulation eliminates the need for physical prototypes and extensive trial-and-error processes. This translates to significant cost savings.
- Time Saving
- Simulation accelerates the design and testing phases, leading to faster development cycles. Engineers can quickly iterate on designs and make improvements without physical constraints.
- Design Optimization
- Simulation allows for the exploration of a wide range of design alternatives and parameter settings to find the most efficient and effective solutions.
- Innovative Solution
- Simulation encourages innovation by enabling engineers to experiment with new concepts, materials, and technologies without the need for extensive physical resources.
- Data-Driven Decisions
- Simulation generates valuable data that can be used to make informed decisions about design modifications, process improvements, and product performance.
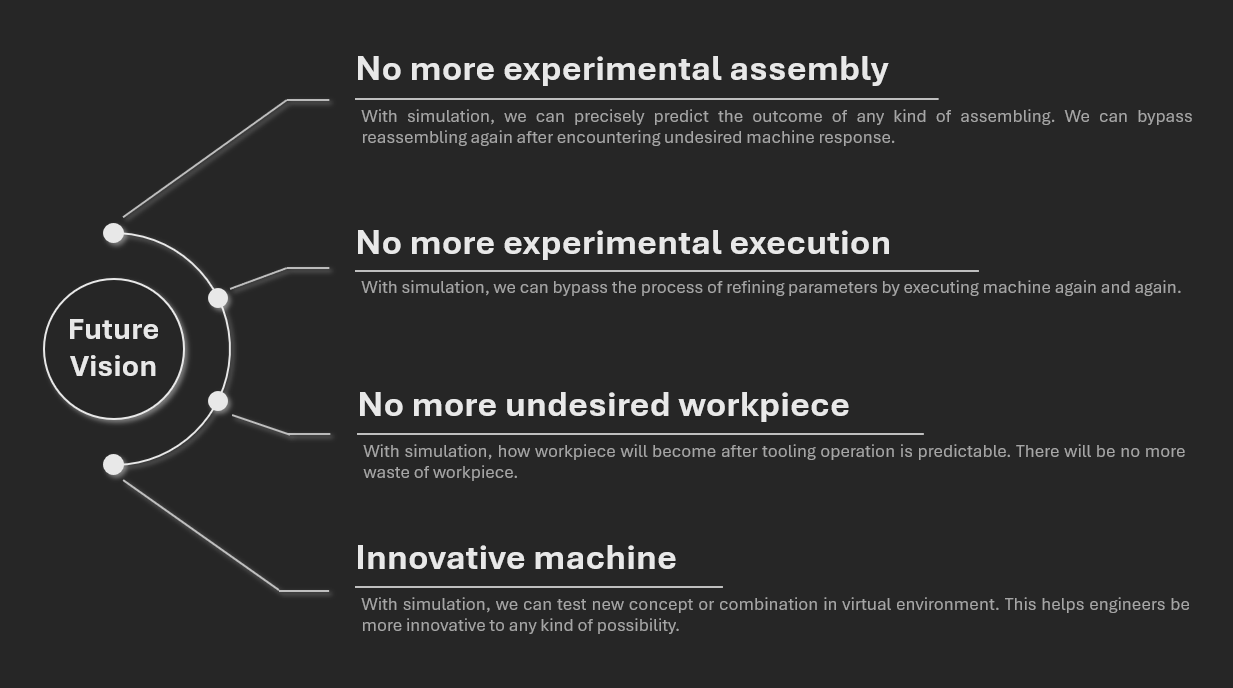
SolidWorks Integration
This feature allows users to directly load their tooling machine models from SolidWorks, automatically extracting all necessary parameters. It eliminates tedious manual input machine parameters, streamlining the setup process and ensuring a smooth workflow.
3D Visualization
Once the SolidWorks assembly is loaded, the tooling machine model is displayed in a 3D environment. This visualization allows users to interact with the model directly, making it easier to select components visually rather than relying on names or lists. With just a few clicks, users can quickly configure machine parameters, enhancing efficiency and reducing setup complexity.
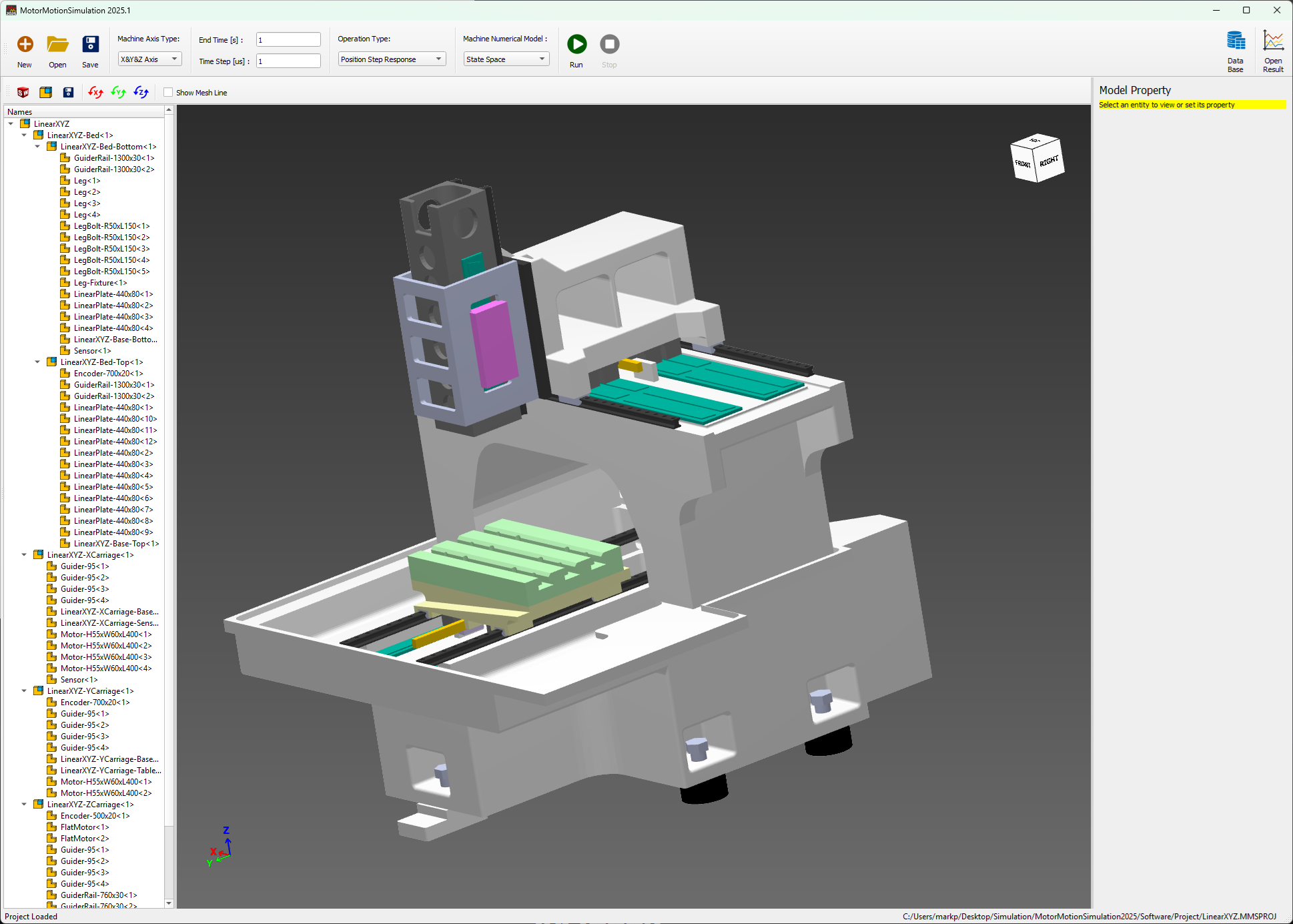
Numerical Model
After the setup is complete, the software generates a numerical model based on the machine configuration. This model is capable of calculating all six degree of freedom states, providing a comprehensive simulation of the machine’s behavior. It supports up to three axes, ensuring flexibility and accuracy for various tooling machine structures.
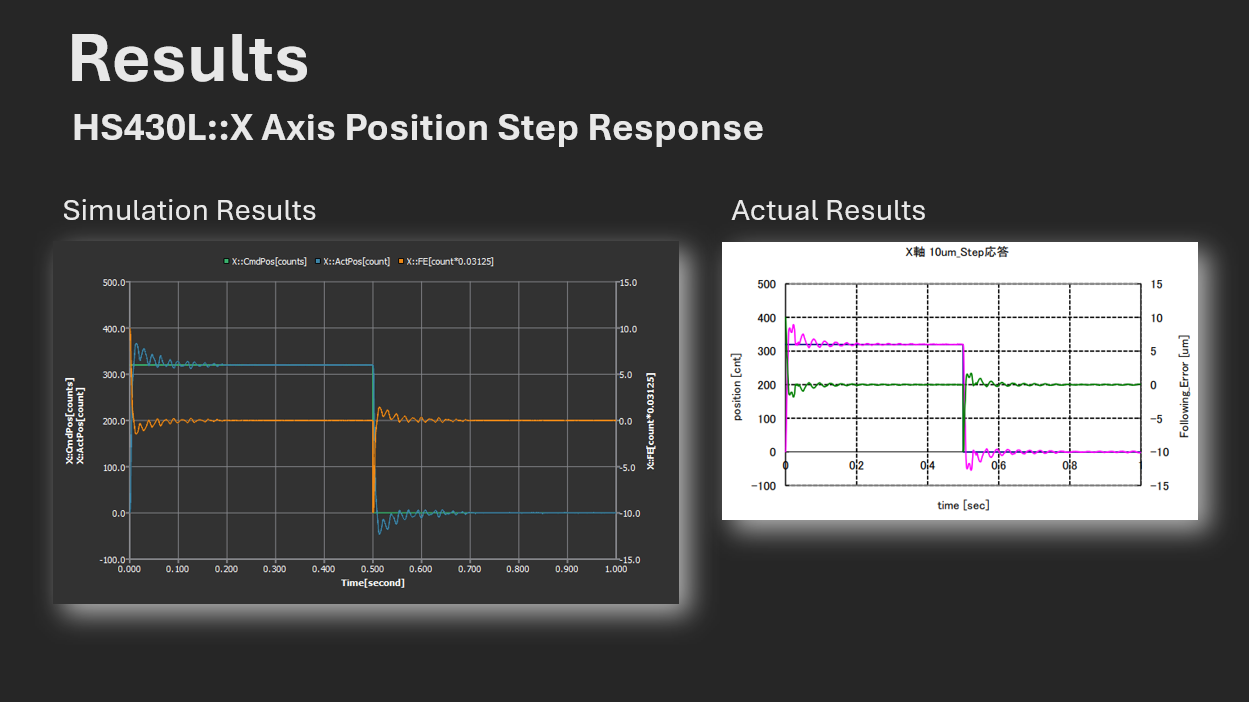
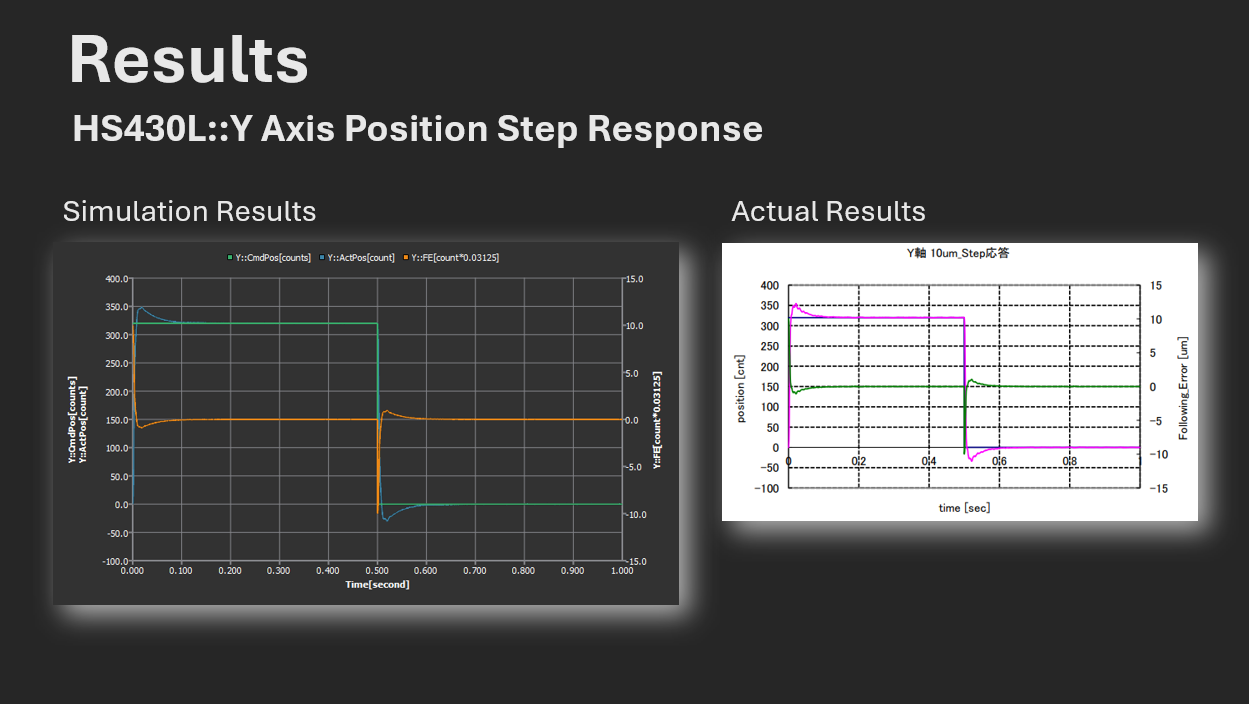
